How Different Types of Plastics Are Manufactured
- DaisyK Ch
- Dec 19, 2022
- 8 min read
Updated: Mar 13, 2023

Plastic plays an essential role in modern life by producing various products, from bags to bottles, kitchenware to home appliances. With its high flexibility, durability, and versatility, plastic has become one of the most commonly used materials to make the production process cost-efficient and time-saving. But most of the time, we have no idea how plastic parts are made, how the manufacturing process works, or why we need to look at these.
Plastic parts manufacturing contains a variety of techniques that provide various advantages to be a good fit for any application. For product designers and purchasers in small and medium enterprises(SMEs), it is crucial to be well acquainted with the manufacturing options available today and how parts can be made tomorrow to determine the best manufacturing process for your product. Hence, this guide serves as an overview of the most widely used plastic parts manufacturing process; read on to find out the features, the techniques involved, and how eziSourcing can help!
How to Choose the Right Plastic Manufacturing Process
Form of the Product
You are first considering whether your parts have sophisticated internal features, tight tolerance requirements, or a high level of geometric complexity first. These factors will be the key determinants in choosing the manufacturing process. For instance, if you have diverse solid products like automotive components or household items to be manufactured, you may focus on injection molding. Or if your industrial plastic parts require a specific process, design for manufacturing (DFM) may help to make them economical and efficient to produce.
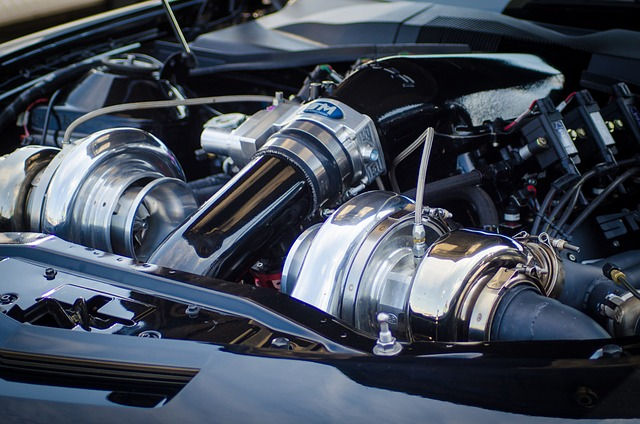
Volume and Costs
Which plastic manufacturing process is the perfect match depends on the total volume of the plastic parts you are planning to manufacture. The difference between the break-even point of the different manufacturing processes is that some of the processes demand high upfront costs due to expensive molding machine investments at first, yet the cost per part decreases when volume increases. On the contrary, although low-volume production requires lower initial costs, the cost per part can become larger since more manual labor may be involved when volume increases.
Production Lead Time
Since production time varies significantly across processes, bearing a clear timeline on the product deadlines helps you determine the best-suited manufacturing process. For some processes, plastic parts can be produced within 24 hours, while others may take months to create a high volume of parts as they require complicated tooling equipment set up in the beginning. Therefore, gaining a comprehensive understanding of how quickly you need the finished goods is key.
Material in Use
Depending on the functionality and aesthetic requirements of your final product, the material used in the manufacturing process may not be the same. Also, types of plastic suitable for plastic manufacturing processes are limited as costs, volume, and lead time must all be balanced throughout the business operation. We suggest that you take the characteristics of your application into account first and then compare them with the plausible choices given below.

Main Types of Plastics
Plastics are mainly composed of high molecular weight raw materials; by adding different additives, they can be formed as thermoplastics and thermosetting plastics to produce various applications.
Thermoplastics
Thermoplastics are formulated from a collection of linear molecules that can move freely at high temperatures. The main attribute of them is that they are so flexible that they are able to melt by heating and back to solidification while cooling down. With the ability to go through this cycle numerously, it is feasible to reuse and recycle thermoplastics.
Here are the most commonly used materials to make thermoplastics:

Thermosetting plastics
In contrast with thermoplastics, thermosetting plastics are created by reticulated structure, which forms irreversible chemical bonds while heating, making them unable to reform after the curing process. Since the internal structure of thermosets will decompose while going through the melt and solidification cycle, they are impossible to be reused or recycle.
Here are the most commonly used materials to make thermosetting plastics:
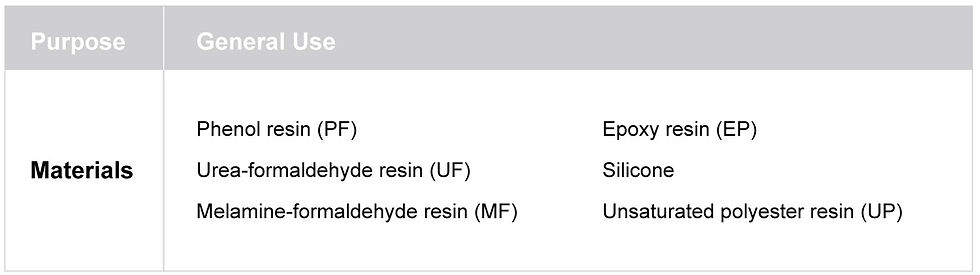
Types of Plastic Manufacturing Processes
Primary Processing
In the process of manufacturing plastic products, different methods are adopted according to different materials and types of products. Primary processing includes the way of making semi-products or products of different shapes and sizes from various forms of plastic compounds. Common processing methods include injection molding, extrusion, blow molding, compression molding, and transferring molding.
Injection Molding
Injection molding is the most common and widely used method of plastic processing. By injecting heated and melted plastic materials into a stainless-steel mold under high temperature and high pressure, the materials will cool and solidify in the mold, and thus the finished part is ejected. Despite the high initial costs of tooling and mold opening, in the beginning, injection molding is the best solution for products with more complex, high-precision structures and high-volume requirements since the cost per part steeply decreases once the mass manufacturing cycle is running.
Applications range from daily necessities to industrial equipment, including high-speed molding for smartphone cases, gas-assisted molding for keyboards and handles, insert molding for all-in-one machines, and interior decorative injection molding for plates and trays.
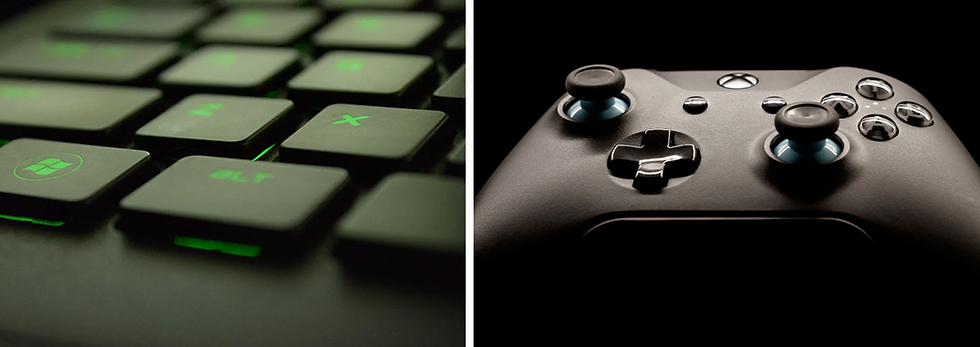
Extrusion
Extrusion works by extruding melted plastics into a tube, rod, sheet, or strip by the rollers of the equipment, cooling, shaping, and then cutting to the desired length. This method is suitable for the continuous manufacturing of long plastic products with a simple structure and a certain cross-section. Because of the simpler internal design, extrusion molding equipment has a rather low unit cost and is widely used.
Extrusion-made parts are mainly used in producing pipes, plates, wires, rods, window frames, etc.
Blow Molding
Blow molding is also known as hollow molding. After the melted plastic is extruded from the mold into a cylinder, it becomes a blank bottle. Then through heated air blown into the bottle blank inside the mold, after cooling down, plastic parts are formed into the required shape. This technique has a high setup cost like injection molding, but through mass manufacturing and continuous production, it results in high production efficiency and low unit costs.
Blow molding is mainly used to create hollow products at scale, including PET bottles, plastic containers, utensils, toys, and industrial parts.

Compression Molding
Compression molding, also referred to as hot compression molding, is usually used for thermosetting plastics. The processing method works by placing the materials on an open, heated mold, and then a plastic part is formed by pressuring and giving the same high temperature toward the mold. This method uses relatively simple instruments and is suitable for the production of heavy parts with no inner chamfers.
Product applications include electrical switches, household appliances, helmets, chairs, car parts, fenders, medium-sized objects with simple shapes, etc.
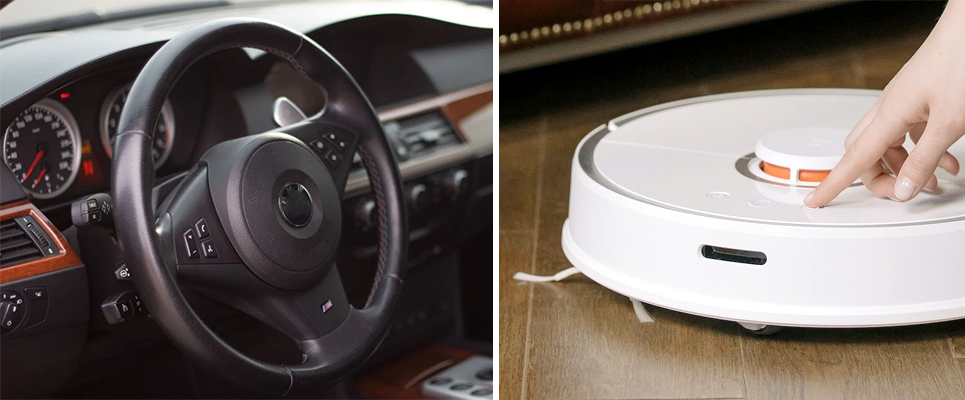
Transferring Molding
Transferring molding is a thermosetting heating method that evolved from compression molding. It is a process in which the heated and softened thermosetting plastic material is transferred under high pressure, and the melted material is passed through the runners and gates into the mold cavities for a hardening reaction. This manufacturing method is suitable for complex and irregular products or products with large variations in the cut surface.
Transferring molding is mostly used in the production of electronic devices such as sockets, capacitors, diodes, connectors, etc.
Secondary Processing
Compared to primary processing, which involves pouring melted plastic materials directly into the equipment to mold them, secondary processing is mainly aimed at reprocessing the molded products to achieve the desired requirements. Secondary processing includes various mechanical processing, mechanical bonding, surface treatment, and chemical treatment methods. The commonly used techniques are as follows.
Thermoforming
After the thermoplastic is heated and softened, the material is molded into a specific shape by adding pressure (known as compression molding) or exerting other external forces such as vacuum (known as vacuum forming), and then cut into the final product after the curing and cooling process is done. The products of thermoforming usually need to be trimmed to cut out and recycle unnecessary parts.
Thin specification thermoforming is mainly used for disposable tableware, containers, lids, etc. Thick specification thermoforming is often used for car doors, dashboards, refrigerator partitions, transportation, furniture, and electronic appliances.
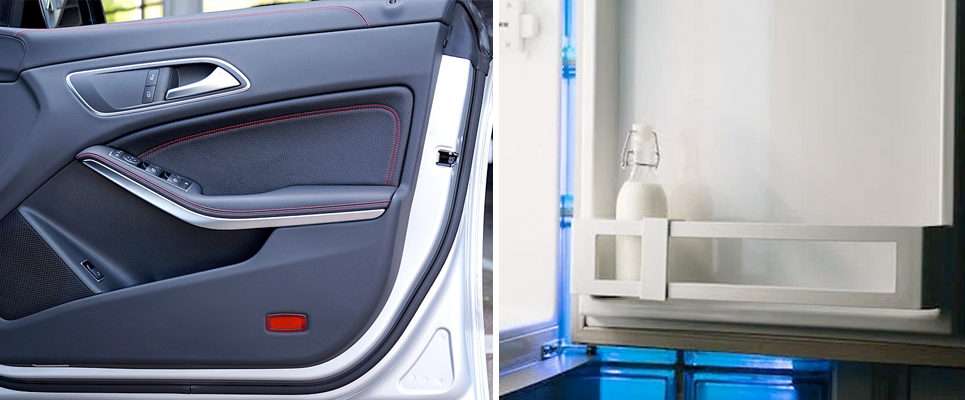
Casting Molding
Casting molding is a process in which a liquid resin is injected into a mold with a hardener. After flowing to the surface of the mold, a plastic part is cured in the mold under normal pressure and then removed.
Casting molding generally does not exert pressure or require high strength of equipment and molds and thus has less restriction on product size. Therefore, the initial investment is low, and large plastic parts with excellent performance can be produced. Nevertheless, since its production cycle is longer, further mechanical processing is required after molding.
Product applications include acrylic board, plate, and other short-run production with low-to-medium volume requirements.
Rotational Molding
Rotational molding, so-called rotomolding, is to first add a quantity of plastic (liquid or powder) into the mold, and after the mold is closed, the material inside will rotate along the two vertical rotational axes to produce large-sized hollow plastic parts.
When the mold is heated, the plastic material inside is gradually and evenly coated to the whole surface of the mold cavity under the action of centrifugal force and heat and thus formed into the same shape as the mold cavity. After cooling and shaping, the desired shape of the product is completed.
Since rotational molding only uses centrifugal force to fill the mold, it requires fewer setup costs, and with its ideal characteristics of producing uniform wall thickness, it is an alternative to blow molding for short-run production. Typical applications of rotational molding are symmetrical hollow objects, traffic cones, steeling wheels, garden planters, and so on.
Plastic Surface Treatment
Silk-screening: A process of making a screen with a specific pattern and then using a squeegee to fill the screen holes with ink to transfer the pattern to the area to be printed.
Hot stamping: The metal part of the stamping paper is covered on the plastic product by a stamping machine under high temperature and pressure to give the surface a metallic character.
Transfer printing: Transferring is done by applying pressure through the intermediate carrier film to transfer the image to the item. This technique is used for more complex shapes.
Welding: A process in which the surfaces of two plastic parts are simultaneously melted by heat and brought together under pressure. There are various ways of welding depending on the heating method and the heat source. Most thermoplastics can be welded, and they can function in the manufacture of doors and windows in buildings, the connection of pipes, as well as in the chemical industry for tanks, vessels, towers, and other devices.
Spraying: A method of pre-treating the surface or interior of a plastic product and then spraying the product with paint. It is suitable for large and uncomplicated surface decoration.
Laser engraving: By going through the optical resonance cavity, the voltage or electric current is able to stimulate active media to create a narrow beam of light, which makes it possible to focus on a small point through the reflective lens precisely and thus vaporize or melt the surface of the engraved plastic products. In this way, words and graphic marks are produced clear and sharp without fading from touching or rubbing, which improves your product identification and texture. For small-volume production, laser engraving can also save the cost of mold opening.
Getting your Plastic Parts Manufacturing Started
The versatility of plastics presents how various and ever-evolving plastic manufacturing processes can be. Therefore, factors including the material, volume, application, and lead time all need to be taken into consideration to choose the right process for your production.
At eziSourcing, we value our customers’ productivity and offer professional consulting services to mold the path to excellence for every young entrepreneur. If you want to learn more about how we work, or if you’re ready to start your project, don’t hesitate to contact us.
Ready to talk? Get in touch with us right here.
Comments