5 Reasons to Use Plastic Injection Molded Products

The five compelling reasons for creating products by means of plastic injection molding are
cost-effectiveness
high quality
durability
precision
design flexibility
Items 2 and 3 are great if you are a consumer. But it’s in relation to items 1, 4, and 5 where the benefits for manufacturers lie.
And if you are a brand looking for a manufacturer with unsurpassed expertise in plastic injection molding production processes, I’ll show you why eziSourcing should be at the top of your short list of candidates.
The Plastic Injection Molding Advantage
When you’re manufacturing a product or a part of a product in large batches, the higher the precision, the better.
Plastic injection molded products can be manufactured rapidly at volume at an extremely high degree of precision which reduces the cost considerably.
And as long as the molds are themselves durably manufactured, any shape can be realized and resolved to extremely fine tolerances over the life of the mold—the more durable the mold, the longer the time between mold replacements and thus the greater reduction in costs.
Additionally, a wide range of types of plastic are suitable for use in the injection molding process and a wide range of methods can be applied including overmolding for example.
Making multi-cavity injection mold parts—where several different parts are made during one production cycle—is also possible.
Injection molding also has an advantage over CNC subtractive manufacturing methods in that a factory is left with minimal scrap. And the need to carry out post-molding finishing operations is vastly reduced.
One drawback of injection molding is the cost of the mold design, although this is true of any manufacturing process that is based on molds.
When producing complex parts warpage and surface defects are possible outcomes, although the better the design of the parts or components at the outset, the less likely that this will occur.
Our workflow at eziSourcing is designed to minimize the possibility of these kinds of problems.
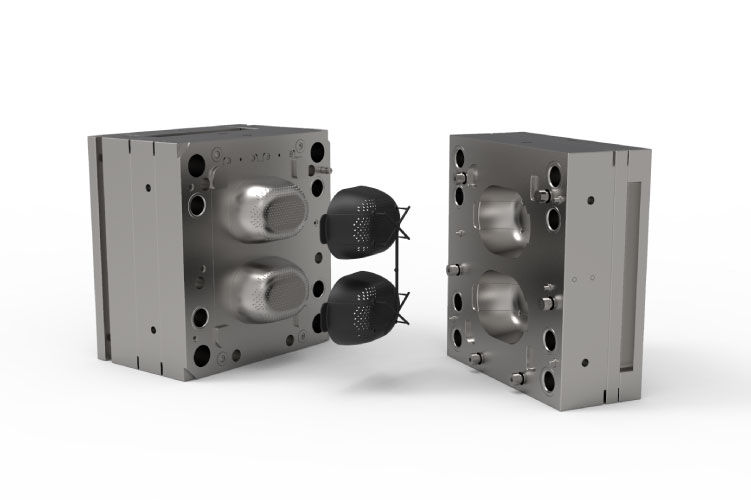
How Does the Plastic Injection Molding Process Work?
The benefit of injection molding is the ability to manufacture a part in large batches with pinpoint accuracy.
The technique itself is simple: melted plastic resin is injected under pressure into a mold. The trick is that the two halves of a mold used for injection must match precisely in order that no seams are visible on an item created using this method.
Functional molds without error are cut out of steel or aluminum to exacting precision using CNC milling and machining methods.
Once the plastic injection molding process of a product commences it’s a matter of repetition.
As long as the mold has been precisely constructed and the component design has also been carefully thought through, there will be minimal product defects
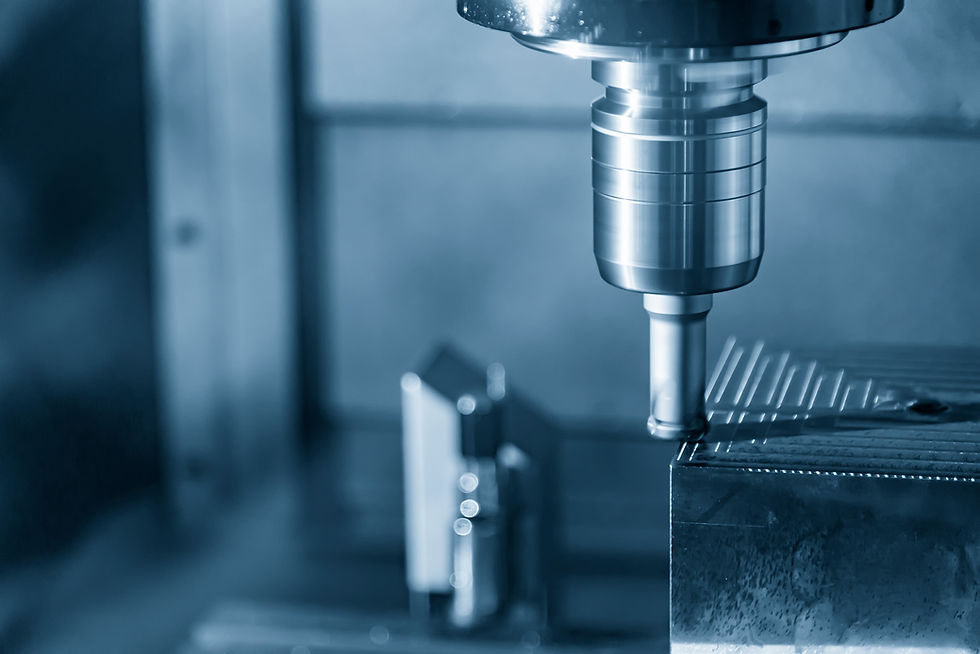
Some Examples of Plastic Injection Molded Products
A plastic injection molding machine can fill just about any mold design quickly, efficiently, and thus cost effectively.
But there are six categories into which most plastic injection molded products fall: 1. electronic housings 2. industrial parts 3. general consumer products 4. sporting products 5. health care products 6. construction materials.
1 Electronic Housings: Nearly every electronic device has some sort of a shell or housing within which contains and protects the electronic circuitry. Products include computer casing, monitors, TVs, smart phones, headphones, telephones, electrical sockets, light switches, circuit breaker switches and hundreds more, most of which are produced by means of plastic injection molding.
2 Industrial Parts: a wide variety of intricate designs can be realized through plastic injection molding, particularly threaded components where, if threads are not exactingly precise, connections cannot be made. Plastic, moreover, is cheaper than metal.
3 General Consumer Goods: Plastic injection molding makes possible a wide variety of intricately shaped products including toothbrushes, packaging of all shapes and sizes, caps for containers of all shapes and sizes, speaker housings, monitor bezels, notebook shells. Plastics such as PET flow easily into injection molds and are perfect for bottles, and especially toys where the injection molding process makes possible the coming of several materials to achieve complex design and color combinations.
4 Sporting Goods: Helmets for biking, skating, mountain climbing as well as protective gear for knees, elbows and other parts of the body are common examples of plastic injection molding products in this category.
5 Health Care Supplies: The most common examples include syringe plungers, the huge range of beakers and tubing, parts used in surgery, as well as enormous variety of implants of both simple and complex shapes that require production in mass quantities.
6 Materials Used in Construction: Plastic together with wood, steel, and concrete are the foundational materials used in building construction. Building out the interior of a house, office complex, or condominium involves cladding panels, cables, pipes and gutters, parts on windows and doors, shutters, floor coverings, and ceiling panels to name a few. Many of these products are mass produced through injection molding.
eziSourcing’s Expertise in Plastic Injection Molded Products Gives You an Unfair Advantage
We are leaders in the plastic injection molding space for two key reasons:
we have decades of collective experience in the creation of plastic injection molded products
we have invested massively in state-of-the-art equipment and machinery
Our machinery includes injection molding machines, high speed molding machines, vertical injection molding machines, and blow molding machines ranging from 120 to 650T.
Plastic injection molding product processing we are extremely familiar with include the
high speed forming of mobile phone casings
gas assisted forming of keyboards
secondary ejection forming of packaging products
interior decorative projecting to make the plates for blow molding
For a full appreciation of our capability be sure to check out this detailed coverage of our approach to tooling, secondary processing, assembling, and quality control.
Ready to talk? Get in touch with us right here.
Comments