8 Effective Methods for Plastic Manufacturing: Boost Your Productivity
- DaisyK Ch
- Feb 24, 2023
- 7 min read
Updated: Mar 13, 2023

Plastics figure prominently nowadays, considering their widely-used and reasonably-priced attributes. They are also vital materials for small and medium enterprises(SMEs) to generate profits efficiently in the complex plastic industry. Thus, to help you better grasp the plastic product manufacturing processes, this article provides the top 8 methods for plastic manufacturing. Check below to figure out how the processes work, the pros and cons of each technique, and their most common applications.
Injection Molding
How It Works
Injection molding is one of the most critical processes for mass-producing objects from thermoplastic materials. The first stage of injection molding is the creation of molds, most of which are made of metal, usually aluminum or steel, and are precision machined to match the properties of the product they are to produce.
The plastic polymer is first fed into a heated barrel and screw when production starts. The molten plastic material is then stirred by the screw rod at a specific temperature.Then, the plastic molded part is injected into the mold cavity under high pressure, cooled and hardened, and then de-molded to obtain the finished plastic product.
Pros and Cons
Pros: The variety of shapes that can be formed, low labor costs, high productivity, smooth and excellent surface finishes, no need for secondary processing, recyclability, and wide range of applications.
Cons: High overall production cost, only suitable for mass production, the high running cost of the injection molding machine, and different parts may have particular requirements for the injection molding process and material.
Applications
Injection molding is the most prevailing method for manufacturing plastic parts, especially in high-volume production. The technique is ideal for various applications with the repeated manufacturing process, including electrical parts, plastic packaging, bottle caps, toys, housewares, mechanical parts, and automotive components.

Extrusion
How It Works
Extrusion molding is the process of melting the raw material pellets into a fluid state and mixing them with additives, then extruding them into the mold hole to form a continuous tube shape. The steel dies that the plastic passes through during extrusion molding determine the section shape of the tube; however, since it is easily deformed at high temperatures, it needs to pass through the forming die again for cooling and hardening. After completion, the product can be directly segmented and packaged.
Pros and Cons
Pros: High production efficiency, low unit cost, and wide range of product specifications and types.
Cons: The plastic parts cannot be very complex or manufactured with high precision.
Applications
Extrusion molding equipment is low-cost, widely used, and easy to automate production. It mainly produces tubes, plates, rods, and films, commonly used for long continuous products such as water pipes, plastic sheets, plastic strips, and cables.

Blow Molding
How It Works
Blow molding, also known as hollow molding, is a process in which the plastic is melted into a flowing state at the beginning. Then the plastic material is placed inside the mold and inflated by air pressure so that it can be molded against the inner wall of the mold, making the product hollow. After cooling,the finished plastic product is produced.
Pros and Cons
Pros: Low initial cost, fast production, and the ability to mold complex parts and grips in the design.
Cons: Limited to hollow parts made from thermoplastics, low strength, and non-recyclable due to the use of multi-layer blanks of different materials to increase barrier properties.
Applications
Blow molding is mainly used to produce thin-walled, hollow products in the form of bottles and inexpensive, bulky products. The applications include packaging for seasonings, PET bottles, detergents, shampoos, and larger products such as garbage cans, gasoline cans, and even chemical drums with a capacity of up to one ton for transporting fishery products.
Thermoforming
How It Works
I. Compression Molding
Compression molding, also known as hot compression molding, is commonly used for thermosetting polymers. The plastic pellets are preheated and placed into an open mold cavity at first, and the mold is closed with a top. At the same time, pressure is applied to force the material into all areas of the mold, and the heat and pressure will continue until the material hardens. Once cured, the molded product can be removed, and the desired shape of the plastic product can be obtained.
II. Vacuum Forming
Vacuum forming starts by heating the plastic sheet evenly until it softens, and then the machine will let the plastic sheet and the mold fit closely and draw out the air to form a vacuum. By doing so, the plastic sheet can be wrapped tightly around the mold, and then the plastic part is available after cooling and setting.
Vacuum molding is a low-pressure process, so there are few restrictions on the material of the mold, and it is suitable for sampling and mass production. For small quantities, wood or plaster can be used as the mold, and epoxy resin or wear-resistant aluminum is used for medium to large amounts.
Pros and Cons
Pros: Short production cycle, high production efficiency, high dimensional accuracy, easy trimming of burrs, and less deformation of inserts and cores, especially suitable for producing inlay products.
Cons: The mold cost is relatively high, and the residual material in the mold cavity, gate, and runner cannot be recycled, so the unit consumption of raw materials is slightly higher.
Applications
Compression molding makes automotive components such as hoods, fenders, spoilers, and more minor, complex features. It is also widely used to produce sandwich structures, such as honeycomb or polymer foam, and is often used to manufacture glass fiber-reinforced plastics. For vacuum molding, the method can be used for all thermoplastic sheets. The most common ones are PS, ABS, acrylic, PC, and typical applications are bakeware, bathtubs, packaging materials, furniture, car interiors, etc.

Casting Molding
How It Works
Casting molding involves introducing and curing liquefied plastics such as monomers, powders, or solvent solutions into a mold. They are converted from liquid to solid by evaporation, chemical action, cooling, or external heat. The finished product can be removed from the mold once it has solidified.
In contrast to extrusion, casting molding relies on atmospheric pressure to fill the mold rather than utilizing an external force to push the plastic into the mold cavity. Since casting molding does not apply force, it does not require high strength of equipment and molds, has less restriction on product size, and has low internal stress in the product. Nevertheless, although casting molding is relatively inexpensive with little initial investment, the thermoset polymers as materials are typically more costly than thermoplastics, and casting molding is also labor-intensive. Since each casting part requires post-processing, the final cost per part is higher than automated production methods such as injection molding.
Pros and Cons
Pros: Less restriction on product size and low initial investment cost.
Cons: A longer production cycle and further mechanical processing are required, resulting in a higher cost per part.
Applications
Casting molding is a suitable method for making small functional plastic parts, especially high-quality prototypes, for low-volume, short-run production. This technique is commonly used for toys, automotive components, dental equipment, and jewelry applications.

Rotational Molding
How It Works
Rotational molding starts by placing a quantity of molten plastic into a heated two-piece closed mold, then rotating the mold to distribute the material evenly on the mold walls, and then opening the mold to remove the finished product after solidification. During the process, air or water is used to lower the temperature, and the finished product must be a hollow structure. Because of the rotation, the final part has a soft curve, which is unsuitable for small and delicate components.
Pros and Cons
Pros: The mold design is relatively simple, the manufacturing cost is low, and the finished part has no seams, making the product very strong and durable.
Cons: The finish of plastic parts is only average, so it is unsuitable for precision molding.
Applications
Rotational molding is suitable for short-term, economical production of large, complex shapes with a symmetrical center axis and uniform wall thickness. Water, chemical, and fuel storage tanks, refrigerated containers, garbage bins, furniture, ceramic planters, lighting fixtures, and water tower equipment can all be made by rotational molding.
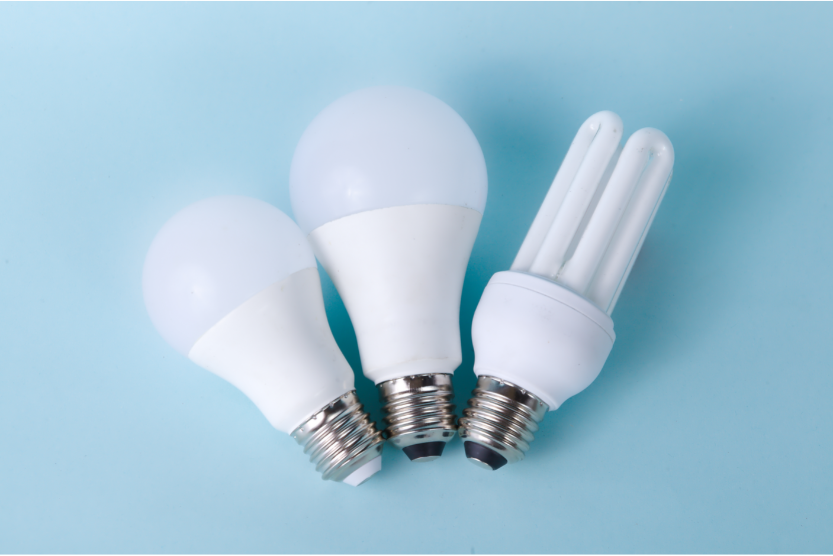
Welding
How It Works
Welding is a process using heat to melt thermoplastic and join plastic objects with metallic tools. The welding methods can be divided into contact and non-contact types; the former one is usually friction welding, and the latter one can be ultrasonic, laser, infrared, or gas convection welding.
I. Friction Welding
The principle of friction welding is that two plastic objects rub against each other quickly under a certain pressure, amplitude, and frequency to generate heat, which makes the plastic melt on the joint surface, and then clamps the two together to complete the joining process. Materials including thermoplastic and semi-crystalline resins (such as HDPE, PA, and PP) are good fits for friction welding.
II. Ultrasonic Welding
Ultrasonic plastic welding uses piezoelectric ceramics to convert electrical energy into mechanical energy, and the welding horn vibrates at a high ultrasonic frequency to produce high heat energy and melt the two plastic surfaces under moderate pressure. Keeping on the welding process under proper pressure can make a completely watertight and airtight fusion achievement.
Pros and Cons
Pros: The welding seam is firm and beautiful, the welding equipment is simple and easy to operate, the technology is widely applicable, and the processing of plastic parts will not produce smoke, dust, and odor, which will not cause pollution to the working environment.
Cons: The one-time investment cost of the equipment is considerable, so it is more suitable for mass production.
Applications
Since welding requires no additional consumables, it is compatible with any shape of the plastic part, making it applicable to a wide range of industries, such as automotive, aviation, agriculture, marine transportation, and plumbing. Typical applications include instrument panels, interior panels, water tanks, gaskets, PVC fences, drainage pipes, faucets, and the embedding of nuts.

Laser Engraving
How It Works
Laser engraving uses voltage or current to pass through an optical resonance cavity to create a narrow beam of light through an active medium excitation. The beam can be focused on a small spot with high precision through a reflective lens to oxidize, discolor, dissolve, or peel off the surface layer to form an image or text. Because of its high speed, pleasing effect, and high quality, laser engraving is suitable for marking minor characters or elaborate graphics.
Pros and Cons
Pros: Permanent marking, waterproof, resistant to heat, sun, and chemicals. Due to the non-contact process, there is no cutting tool wear or damage and no cost of consumables like chemicals and inks. The material remains free of pressure, tension and fixation, thus ensuring consistent and standardized results. The laser engraving machine is easy to operate and requires no pre-processing or post-processing.
Cons: The initial investment cost of the equipment is significant, so it is more suitable for high-volume requirements.
Applications
Laser engraving is used in a wide range of applications, including the electronics industry, medical industry, advertising industry, and art industry. It is most commonly used in engraving labels, product serial numbers, serial numbers, bar codes, QR codes, etc.
Getting your Plastic Parts Manufacturing Started
eziSourcing is a plastic manufacturer with good product design, high innovation capabilities, excellent quality control, and provides plastic manufacturing solutions. We value our customers’ productivity and offer professional consulting services to mold the path to excellence for every young entrepreneur. If you are interested in how we work, or if you’re ready to start your project, don’t hesitate to contact us.
Ready to talk? Get in touch with us right here.
コメント